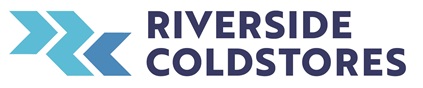
Riverside Coldstores is a family-owned business with more than two decades’ experience handling meat and related products. Their operation utilises 2500+ pallet spaces, 4 blast freezers, 3 loading docks along with various storage rooms.
After spending two fruitless years looking for an alternate provider that supported scanning of meat industry barcodes and associated logistics knowledge, Riverside identified Infoware Services as the logistics technology partner who understood their requirements.
When they engaged with Daryl Northfield, Director of Infoware Services who has 35 years’ experience in helping businesses re-engineer their processes, they found a partner with a clear focus on listening to their needs. This was a combination of understanding their requirements and challenging the status quo for further benefits of using the latest technology.
The Opportunity
Riverside Coldstores required a system that supports their meat industry focused business across 3PL warehousing and transport, replacing their existing software that had become aged, unstable and not offering any improvements.
Number #1 – Riverside needed to implement a robust serial meat carton scanning process with confidence that it would deliver improved speed and accuracy. This scanning process would cover end-to-end needs from unloading, chilling, through to storage and customer order load outs.
They were also acutely aware that their new system must as a minimum:
- Perform carton barcode scanning accurately and quickly for both inward and outward movements
- Provide visibility of transactions via a web portal for their 3PL customers tracking orders, products, production dates and carton serial barcodes
- Deliver automated billing functionality that would replace their existing manual processes
- Have EDI connection capability to ensure retention of their major customers
- Be supported
- Offer updates as business needs and technology change
The Infoware Solution
Infoware further enhanced their 3PL product scanning solution to meet Riverside’s specific operational requirements, utilising serial carton scanning for zero stock picking error potential, combined with quicker and accurate logistics, making sure all cartons picked are within specified production date ranges. Picking of full pallets occurs by a single scan of any unique meat carton barcode on the pallet.
Infoware’s formal control of barcode definitions allows Riverside to define multiple barcode formats for an APN. This is especially useful when their customers deal with multiple meat works or wholesalers. Previously this required multiple product codes for different barcode definitions of the same product, resulting in additional effort and potential errors when having to track artificially created product codes for a single APN.
Utilising Infoware’s various customer ordering options significantly reduces data-entry time. This is achieved with our customer self-service portal for small order volumes, automated order creation from emailed PDF orders for larger volumes, as well as full EDI integration.
The Outcome
Previously it took up to 4 workers 2.5 hours to unload a truck. It now takes 2 workers 40 minutes to unload, receipt and put product away into Infoware WMS (a major efficiency gain in anyone’s language).
With the prior system, if they lost network connectivity during scanning workers had to frustratingly restart scanning from the beginning of the unload. With Infoware, while this has not occurred, if network connectivity was temporarily lost then scanning would resume right from where they were previously.
The ability to interpret emailed customer PDF orders and automatically create the order in Infoware means no more data entry for orders from their major customers – an unexpected benefit when they were looking for a replacement solution.
Lacking logistics visibility tools in the past, James Drake, Operations Manager at Riverside Coldstores went from being apprehensive about using Infoware’s Run Planner, to quickly making it their go-to ‘single source of truth’ tool for managing customer order picks and deliveries. Orders change colour on the Run Planner as staff start picking, through to pick completion, then load outs and deliveries.
Both the Riverside team and their customers have found the Infoware portal to be flexible and easy to use. Customers can also retrieve delivery dockets, POD’s, outward movement advices and serial carton data from Infoware’s customer self-service portal. They have full visibility of stock availability including by production date.
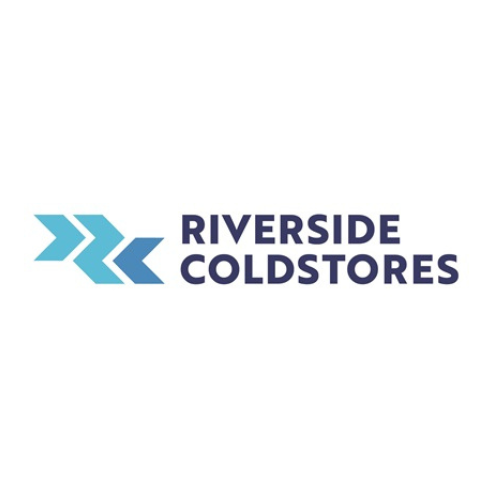
“It used to take 4 staff 2.5 hours to unload a truck and receipt meat carton stock into the warehouse. This now takes 2 staff 40 minutes with Infoware. It now takes 40 seconds to scan each meat carton onto a pallet – with previous system this took a lot longer.
The previous system would drop out and we would have to re-scan from scratch adding to its frustration. Infoware has not dropped out – but I am told if comms did drop out we would continue on from where we left off.”